غلظت دهنده های چاپ در نساجی
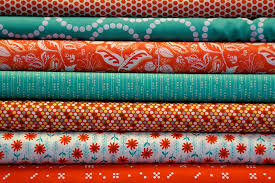
امروزه انواع مختلفی از غلظت دهنده های طبیعی، مصنوعی و امولسیونی در صنایع نساجی بکار می روند. هر کدام از این نوع غلظت دهنده های چاپ نساجی کاربردهای خود را دارا بوده و بر اساس فاکتور های مختلفی از جمله نوع پارچه ، چاپ ، رنگ مصرفی ،کاربرد نهایی و قیمت تمام شده و غیره برای استفاده انتخاب می شوند.
غلظت دهنده های چاپ در صنعت نساجی
چرایی مصرف انواع غلظت دهنده ها در چاپ :
عملیات چاپ پارچه چون بصورت موضعی انجام میشود رعایت مرز طرح از اهمیت ویژه ایی برخوردار است. غلظت دهنده ها با ایجاد مرز مشخص بین طرح ها و جلوگیری از درهم رفتگی رنگ هاست.
در هنگام استفاده از غلظت دهنده ها نکات مهمی را باید رعایت نمود که به شرح زیر می باشد:
- نوع رنگ مصرفی ، روش چاپ و جنس پارچه
- در نظر گرفتن پایداری غلظت دهنده ها در محیط اسیدی و قلیایی بسیار مهم است
- غلظت دهنده مصرفی براحتی بعد از فرایند چاپ از سطح پارچه جدا گردد .
- انتقال سریع رنگینه به داخل الیاف، عدم تداخل رنگهای چاپ، خشک شدن سریع پس از انتقال بروی پارچه و انعطاف پذیری پارچه را تحت تاثیر قرار ندهد.
- انتقال یکسان بروی پارچه ، چسبندگی یکسان رنگ به پارچه
- نفوذ رنگ به داخل پارچه در هنگام بخار دادن.
خمير چاپ معمولاً حاوی 70 - 40 % محلول غلظت دهنده است که از اين مقدار( 10 - 5/ 2%)حداکثر 16 % آن را عامل غلظت دهنده تشکيل می دهد.امولسیونهای روغن در آب، که در گذشته به عنوان غلظت دهنده در خمير های بر پايه مواد رنگزا استفاده می شدند، امروزه با مواد مناسب جايگزين شد ه اند که مزيت آنها انحلال پذيری در آب سرد است.
امولسیونهای آب در روغن نيز در گذشته به عنوان غلظت دهنده در خمير های بر پايه رنگدانه استفاده می شدند. در اين غلظت دهنده ها تا 70 % حلالهای نفتی مخلوط هیدروکربن های آلیفاتیک با طول زنجير C50 – C12 به کار رفته بود که مواد آلی فرار آن حين رنگرزی و خشک شدن در دستگاه ها، وارد هوا می شد. البته هنوز هم در غلظت دهنده های جديد تا حدود 10 % روغن های معدنی می تواند وجود داشته باشد که در نهايت وارد هوا خواهد شد. به همين دليل نسل بعدی غلظت دهنده ها به گونه های توسعه يافت که حاوی هيچ حلال فراری نباشد. اين نوع غلظت دهنده ها به شکل گرانول های عاری از غبار به بازار عرضه می شوند.
غلظت دهنده های صنعت چاپ منسوجات
سالها غلظت دهندها مورد استفاده در صنعت چاپ نساجی عصاره های طبیعی مانند گوار، آلژينات، نشاسته و مشتقات سلولز بودند. از ویژگی های این غلظت دهنده ها می توان به زمان طولانی آبپوشی، پایداری حرارتی ضعیف و درصد خلوص کم اشاره کرد. بنابراین تلاش در جهت بهبود خواص این مواد به عنوان غلظت دهنده از طريق شیمیایی و یا از طريق اختلاط فیزیکی صورت گرفت، اما این مواد محدودیت هایی از قبيل کوتاه و غیره داشتند.غلظت دهنده های طبیعی مورد استفاده در چاپ پیگمنت از لحاظ عمق رنگ،درخشش فام، دوام شستشو و زیردست الیاف نتایج خوبی به دست نمی دهند و همين مسئله منجر به عرضه غلظت دهنده های مصنوعی به بازار گرديد. با عرضه غلظت دهنده های امولسیونی، در چاپ پیگمنت برای سالها از این روش انجام می شد. برای تهيه این گونه غلظت دهنده ها نفت یا حلالهای نفتی و آب با سرعت بالا در همزن و در حضور امولسیفایر با هم مخلوط می شدند، که اين نهایتاً منجر به بالا رفتن گرانروی خواهد شد.در امولسیونهای روغن در آب با وجود کیفیت چاپ عالی ناشی از رنگ دهی مناسب، درخشندگی و زیردست خوب پارچه، مصرف زياد حلال 50%-80 منجر به ایجاد معایب زیر می شود:
-1 نفت و حلال های نفتی میتوانند در حضور هوا مخلو طهای شديداً احتراق پذير تشکیل دهند.بنابراین حمل و انتقال آنها خطرناک است.
-2 استفاده از حلالهای فرار از طریق ورود بخارات آنها به هوا یا مایعات حاوی آنها به رودخانه ها منجر به آلودگی محیط زیست می شود. اخيراً دولت ها قوانین اکيداً سختگیرانه ای را در مورد استفاده از تركيبات حاوي مقادير زياد حلال تصویب کرد ه اند.
-3 افزایش قیمت تمامی محصولات پتروشیمی از جمله نفت باعث شده تا قيمت تمام شده چاپ پیگمنت با اين روش بسیار گران شود. به دلیل محدودیت هایی که در استفاده از غلظت دهنده های امولسیونی از جمله نفت وجود دارد، به تدريج نیاز به استفاده از غلظت دهنده های جایگزین ایمن تر با کاربری آسا نتر و قیمت مناسب تر احساس شد. به این منظور تحقیقات گسترده ای بر روی غلظت دهنده های مصنوعی صورت گرفت و سرانجام غلظت دهنده های مصنوعی تجاری با ویژگی های بسيار مناسب به بازار عرضه شدند.
انواع غلظت دهنده های چاپ پارچه
|
|
غلظت دهنده ها |
مصرف |
پلی ساکاریدهای اصلاح نشده غیر یونی |
|
نشاسته گندم، ذرت و برنج |
امروزه کم استفاده میشود. |
صمغ عربی |
امروزه کم استفاده میشود. |
صمغ تراگاکانت |
امروزه کم استفاده میشود. |
آرد گوار(بسیار ریز) |
چاپ فرش |
پلی ساکاریدهای اصلاح شده غیر یونی |
بصورت محدود استفاده می شود |
محصولات نشاسته ای: صمغ انگلیسی نشاسته های متورم شونده |
با غلظت بین 30-50% ارائه شده و در برابر قلیاها این مواد مقاومت بالایی دارند. |
اترهای نشاسته غیریونی و استرهای نشاسته غیر یونی |
در فرمول های ترکیبی، به عنوان چسب برای منسوجات پشمی سلولزی مورد استفاده قرار می گیرند. |
رزین صمغی: صمغ کریستال صمغ صنعتی (مثل کوردوفان) |
به دلیل قیمت بالا در ترکیب با سایر مواد و یا در مواردی که غلظت دهنده ای با کیفیت بالا مورد نیاز است مورد استفاده می باشد. |
گالاکتومانان ها (پلی ساکاریدها): مشتقات گوار |
امروزه مصرف این نوع گوار افزایش پیدا کرده است . |
مشتقات سلولز: مشتقات متیل مشتقات اتیل مشتقات هیدروکسیل مشتقات هیدروکسی پروپیل |
استفاده از این مواد به شدت توصیه می شود ولی بندرت به تنهایی مورد استفاده می گردد. قبلا از این ماده به عنوان تثبیت کننده برای غلظت دهنده های امولسیونی شامل حلال های نفتی (مثل وایت اسپریت) استفاده می شد. |
پلی ساکاریدهای آنیونی |
|
آلژینات ها:
آلژینات سدیم آلژینات منیزیم آلژینات آمونیوم |
امروزه در چاپ های راکتیو بسیار کاربد دارند . قیمت این نوع غلظت دهنده به شدت افزایش داشته و بروی قیمت تمام شده کالای چاپ شده نهایی تاثیر گذار می باشد. |
پلی ساکاریدهای کربوکسی متیله شده: اترهای نشاسته ای آنیونی آرد های بذر آنیونی اتری شده کربوکسی متیل سلولزها و نمک های سدیم آنها |
اساساً بر پایه گوار بوده و به تنهایی یا در ترکیب با سایر مواد بکار می رود. |
زانتان (پلی ساکارید طبیعی) |
تولید این ماده از طریق تخمیر کنترل شده گلوکز انجام میشود. در فرش های ضخیم کاربرد دارد. با افزودن مواد کمکی بخصوص در خمیر چاپ، می توان به سازگاری بین زانتان و مواد رنگزای کاتیونی، در ترکیب با سایر مواد مثل محصولات آرد بذر دست یافت |
عوامل پلیمری مصنوعی |
|
پلی اکریلیک اسیدها |
تنها غلظت دهنده مصنوعی با اهمیت که امروزه مورد استفاده قرار می گیرد. |
محصولات همبسپارش انیدرید مالئیک(اتیلن، استایرن، یا وینیل متیل اتر با مونومرهای چندعاملی مثل دی وینیل بنزن) |
این مواد اهمیت چندانی ندارند. |
امولسیون های آبی همبسپارهای 20-40% متاکریلیک اسید، ترکیبات الفینی (مثل اتیل اکریلات) و 2% مونومر های چندعاملی |
این مواد اهمیت دارند. |
با توجه به جدول بالا و تقسیم بندی اولیه ارایه شده برای انواع غلظت دهنده ها در زیر توضیحات بیشتری در مورد انواع مختلف غلظت دهنده ها ارایه می گردد :
انواع غلظت دهنده ها مصرفی نساجی :
1- غلظت دهندههای طبیعی
- آرد دانه اقاقیا
آرد دانههای اقاقیا که از درخت کاروب (carob) گرفته میشود از زنجیرههای اصلی متشکل از دی.مانوز (D-mannose) و زنجیرههای انشعابی گالاکتوز تشکیل شده و دارای وزن مولکولی حدود ۳۱۰۰۰۰ میباشد. آرد دانه اقاقیا در آب سرد به آسانی حل نمیگردد و جهت حل نمودن کامل آن به حرارت احتیاج است. این غلظت دهنده يك پلیساکارید آنیونی میباشد و ۱۱-۳ :PH اثر کمی بر غلظت آن دارد تنها با استفاده از ۲ درصد ماده جامد آن ویسکوزیته مناسب ایجاد میگردد. نمكهای سدیم اثر کمی بر ویسکوزیته آن دارد.
آرد دانه اقاقیا هم با بوراتها تولید کمپلکس نموده و ایجاد ژل میکند که در چاپ دو مرحلهای با رنگینههای خمی مورد استفاده قرار میگیرد (بر اثر اضافه نمودن اسید، غلظت دهنده به حالت اولیه خود باز میگردد).
صمغهای گیاهی
این غلظت دهندهها که به صورت شیرهای از تنه درخت و یا بوته گرفته میشود پلی ساکاریدهای کمپلکس است که هر یک دارای گروههای اورونیک اسید (Uronic Acid) متفاوت میباشد.
- کتیرا
کتیرا یك پلی ساکارید متشکل از گالاکتوز، فروکتوز (Fructose)، زیلوز (Xylose)، آرابینوز (Arabinose)، رامنوز (Rhamnose) و گلوکورونیک اسید (Glucuronic Acid) است که حلالیت خوبی در آب داشته و تولید محلولهای غلیظ مینماید.
کتیرا در آب ایجاد محلولهایی با ۶-۵:PH مینماید. این محلولها در محیطهای اسیدی تا ۲ :PH پایدار میباشد ولی ویسکوزیته آن بر اثر افزایش حرارت و افزودن نمک به آن کاهش مییابد. کتیرا در جنوب غربی اروپا، یونان، ترکیه، سوریه و مرغوبترین نوع آن (جهت مصرف غذائی) در ایران یافت میشود. کتیرا پس از ۶ ساعت در آب گرم متورم میگردد. محلول ۴ تا ۵ درصد کتیرا به عنوان غلظت دهنده دارای ویسکوزیته مناسب است.
- صمغ عربی
صمغ عربی از درخت اقاقیای سنگالی گرفته میشود که در سودان، نیجریه و آفریقای غربی وجود دارد. این غلظت دهنده مخلوطی از نمک کلسیم، پتاسیم و منیزیم آرابین است. آرابین (Arabine) یک پلیساکارید کمپلکس متشکل از واحدهای گلوکورونیک اسید، ارابينوز، رامنوز و گالاکتوز میباشد و در آب حلالیت خوبی دارد.
- صمغ کریستال
این غلظت دهنده نوع خالصتری از صمغ کارایا (Karaya) میباشد و به راحتی در آب حل میگردد.
صمغ کارایا دو مرتبه در سال از درخت Sterculia Urens»» گرفته میشود و کشور هند تولید کننده اصلی آن میباشد. کیفیت صمغ تولید شده در اوایل تابستان بهتر از صمغ گرفته شده برای نوبت دوم در سال میباشد. صمغ کارایا بعد از خشک شدن به صورت پودر به بازار عرضه میشود.
صمغ کارایا یک پلیساکارید با وزن مولکولی زیاد میباشد (۱۰۹×۵/۹) که بخشی از آن به صورت استیله شده است. این صمغ دارای ال رامنوز (L-Rhamnose) و همچنین دی گالاكتوز (D-Galactose) و دی گالاکتورونیک اسید (D-Galacturonic Acid) بوده و در مقایسه با صمغهای دیگر دارای حلالیت کمتری در آب میباشد (در آب کاملا حل نمیگردد) ولی در آب به خوبی متورم میگردد. ویسکوزیته این غلظت دهنده با افزایش حرارت و تغییرات PH کاهش مییابد.
محلول کارایا (۱۸-۱۵ درصد) که به کمک حرارت تهیه میگردد به عنوان غلظت دهنده در صنعت چاپ مورد استفاده قرار میگیرد. این صمغ در صنعت غذائی هم کاربردهای زیادی دارد.
- آلجینات ها
غلظت دهندههای آلجينات، نمكهای سدیم، پتاسیم و یا کلسیم آلجينيك اسید (Alginic Acid) میباشد که خود يك پلی ساکارید خطی متشکل از واحدهای بتا. دی . مانورونیک اسید (B-D- Mannuronic Acid) و ال گلوکورونیک اسید (L-Guluronic Acid) میباشد و از جلبك دریائی بدست میآید. این غلظت دهنده در آب سرد و گرم حل میگردد و تولید محلولهای غلیظ میکند که با نمك کلسیم ایجاد ژل مینماید.
نمكهای آلجينات قادر است تا ۳۰۰ برابر وزن خود آب جذب نماید و حتی بعد از تثبیت در دمای بالا، دارای حلالیت جذب در آب میباشد این نوع غلظت دهنده به علت دفع گروههای آنیونی رنگینهها توسط گروههای کربوکسیل یونیزه شده در محیط قلیائی، برای ساخت خمیر چاپ رنگینههای راکتیو بسیار مناسب میباشد.
غلظت محلول آلجيناتها با افزایش درجه حرارت کاهش یافته و در صورتی که برای مدت زیاد در حرارت بالا نگه داشته نشود پس از سرد شدن مجدداً به حالت اولیه باز میگردد (در حرارت بالا و مدت زمان طولانی، طول مولکولهای زنجیرهای کوتاه میگردد).
غلظت محلول آلژینات در ۱۰-۵:PH تغییر نمینماید ولی در PH کمتر از ۵/۴، افزایش مییابد. در ۳ :PH غلظت دهنده آلژینات رسوب نموده و در PH بیش از ۱۰ به ژل مبدل میگردد.
پروپیلن گلیکول آلژینات در ۳-۲ :PH با ثبات است ولی در PH بیش از ۵/۶ ثبات خود را از دست میدهد.
ویسکوزیته محلول نمكهای آلجينات تحت تاثیر جرم مولکولی آنها قرار دارد. محلولهای ۲ درصد نمكهای آلجينات با جرم مولکولی بالا و نیز محلولهای ۶ درصد نمكهای آلجينات با جرم مولکولی پایین ویسکوزیته کافی دارد.
2- غلظت دهندههای نیم مصنوعی
منبع اصلی غلظت دهندههای نیم مصنوعی چوب میباشد که سلولز آن بازیافته شده و بعد از انجام واکنشهای شیمیایی لازم، موادی مثل متیل سلولز، اتیل سلولز و کربوکسی متیل سلولز (C.M.C) (Carboxy Methyl Cellulose) تولید میگردند. این مواد بیشتر به عنوان آهار در صنعت نساجی مورد استفاده قرار گرفته و در مواردی به عنوان غلظت دهنده به کار گرفته میشوند.
3- غلظت دهندههای مصنوعی
عدم اطمینان از موجود بودن همیشگی غلظت دهندههای طبیعی به مقدار کافی و همچنین مسائل مربوط به محیط زیست در رابطه با کاربرد امولسیون به عنوان غلظت دهنده باعث پیشرفت در استفاده از پلیمرهای مصنوعی به عنوان جانشینی برای غلظت دهندههای طبیعی و امولسیون شده است.
یکی از غلظت دهندههای مصنوعی پلی وینیل الکل (Poly vinyl Alcohol) میباشد که به مقدار محدود جهت تولید غلظت دهنده برای چاپ پارچههای نایلونی به کار گرفته شده است. برای حصول ویسکوزیته مناسب مقدار تا ۲۰ درصد از آن مورد احتیاج میباشد. کوپلیمرهای آکریلیک اسید، متاکریلیک اسید و متاکریلات به مقدار ۱ تا ۲ درصد ویسکوزیته مناسب را ایجاد میکند.
از آنجایی که مقدار کمی از غلظت دهندههای مصنوعی خشك تولید ویسکوزیته مناسب میکند. این نوع غلظت دهندهها در مواردی که پارچه بعد از چاپ شسته نشود (چاپ با رنگدانهها) بسیار مناسب میباشد.
خرید غلظت دهنده مصنوعی کلیک نمایید
4- غلظت دهنده امولسیون (Emulsion)
تعليق باثبات دو و یا تعداد بیشتری از مایعات غیرقابل امتزاج، امولسیون نام دارد که به کمک میکسرهای قوی تهیه میگردد. ثبات امولسیون توسط امولسیفایر (امولگاتور) (Emulsifier (Emulgator)) تضمین میگردد. یکی از مایعات تشکیل دهنده امولسیون، آب و یا یک محلول آبی است، مایع دیگر روغن و یا یك مایع غیر قابل امتزاج دیگری با آب میباشد. چنانچه روغن در داخل آب به صورت معلق در آورده شود روغن فاز داخلی (دیسپرس) و آب فاز خارجی (پیوسته) میباشد و امولسیون حاصل، روغن در آب (o/w) گفته میشود. در صنعت چاپ، بیشتر از امولسیون روغن (نفت) در آب استفاده میشود که میتوان آن را به كمك آب رقیق نمود.
امولسیفایر که باعث کاهش کشش سطحی بین آب و روغن میگردد، معمولا يك مولكول زنجیرهای طویل میباشد که دارای يك بخش آب دوست و يك بخش چربی دوست میباشد که با جهتگیری به طرف روغن و آب، امتزاج این دو را ممکن میسازد. معمولا مایعی که امولسیفایر، بیشترین حلالیت را در آن دارد فاز خارجی را تشکیل میدهد. به عنوان مثال صابونهای فلزات قلیائی، امولسیون روغن در آب و رزینهای محلول در روغن تولید امولسیون آب در روغن مینماید. امولسیفایرها ممکن است به صورت يك پوشش برای روغن عمل نموده و از به هم رسیدن ذرات روغن و در نتیجه شکست امولسیون جلوگیری کند (پروتئینها).
حلالیت نسبی یک امولسیفایر در آب و یا روغن توسط توازن هیدروفیل (آب دوستی). لیپوفیل (چربی دوستی) B.H. L نشان داده میشود که به ساختمان شیمیائی و مقدار یونیزاسیون آن بستگی دارد. B.H. L بین ۱ تا ۲۰ متغیر میباشد. امولسیفایرهای آب دوست قوی دارای B.H. L بالا میباشد. امولسیفایرهای با B.H. L پائین (۳تا ۶) برای تولید امولسیونهای آب در روغن و انواع با B.H. L بالا (۸تا ۱۸) برای تولید امولسیونهای روغن در آب مناسب میباشد.
در امولسیون اندازه ذرات فاز داخلی بین ۱۰۰ تا ۷۰۰۰ نانومتر متغیر میباشد. با کوچکتر شدن اندازه ذرات، ویسکوزیته امولسیون افزایش مییابد. رنگ امولسیون به اندازه ذرات بستگی دارد. معمولا با کاهش اندازه ذرات و غلیظتر شدن امولسیون، رنگ سفید خامهای آن به رنگ سفید با ته رنگ آبی تغییر پیدا میکند. بهعلاوه ویسکوزیته امولسیون همچنین به مقدار و نوع امولسیفایر بستگی دارد. امولسیفایر های آنیونی، قادر به تولید ویسکوزیته بیشتری در مقایسه با انواع غیر یونی میباشد.
در خشک کردن پارچه چاپ شده، نفت و آب تبخیر شده و غلظت دهندهای روی پارچه باقی نمیماند. غلظت دهندههای امولسیونی، علیرغم ساده بودن تهیه آنها و باقی نماندن روی پارچه و همچنین عدم احتیاج، به شستشو بعد از تثبیت، هوا را آلوده ساخته و خطر آتش سوزی آنها زیاد میباشد. از این رو در بعضی از کشورها، استفاده از امولسیون صد در صد (تمام امولسیون) ممنوع شده و امولسیون بایستی با غلظت دهنده دیگری مثل آلژينات به نسبت ۱:۱ مخلوط گردد. این مخلوط، نیم امولسیون خوانده میشود. لازم به تذکر است که خارج ساختن مؤثر بخار نفت و آب از خشك كن، جهت جلوگیری از آلودگی محیط کار و آتش سوزی ضروری است. با غلظت دهنده تمام امولسیون، معمولا خطوط مرزی صاف حاصل نمیشود زیرا حرکت نفت باعث انتقال بخش کوچکی از رنگینه به خارج از محدوده چاپ میگردد. اضافه نمودن ۵۰ تا ۱۰۰ گرم آلژينات و یا کتیرای حدود ۴ درصد به غلظت دهنده امولسیون از حرکت مولکولهای رنگینه به خارج از خطوط مرزی به میزان زیادی جلوگیری مینماید.
انتخاب غلظت دهنده با توجه به نوع رنگینه
۱. راکتیو
غلظت دهندههای آلجينات، امولسیون
۲. دیسپرس
صمغ کریستال، مشتقات آرد دانههای گیاهی، مخلوط آلژينات و اتر نشاسته
٣. خمی
A. روش پتاس - رنگالیت
نشاسته، اتر نشاسته و آرد دانههای گیاهی مخلوط کتیرا و نشاسته
B. روش دو مرحلهای
آلژینات، نشاسته – اتر نشاسته و آرد دانههای گیاهی
۴. اسیدی و متال کمپلکس
صمغ کریستال و آرد دانههای گیاهی
۵. کرمی
غلظت دهندههای مقاوم در مقابل کرم از آرد دانههای گیاهی و مخلوط غلظت دهنده نیم امولسیون با همین غلظت دهندهها
۶. نفتلی
آلجيناتها، آرد دانههای گیاهی و مخلوط نشاسته کتیرا
۷. خمی محلول
مخلوط نشاسته کتیرا و آرد دانههای گیاهی
۸. کاتیونی
صمغ کریستال، چسب انگلیسی و آرد دانههای گیاهی
۹. رنگدانه (پیگمنت)
غلظت دهنده امولسیون و مصنوعی
۱۰. چاپ برداشت
چسب انگلیسی، صمغ کریستال، مخلوط نشاسته کتیرا و آرد دانههای گیاهی
اسامی تجاری غلظت دهندهها و نوع آنها در بخش ضمیمه آورده شده است.
آماده سازی غلظت دهنده
غلظت دهندهها معمولا چند ساعت قبل از به کار گرفته شدن آماده می گردد. به این ترتیب تورم آنها در موقع به کار گرفته شدن کامل میشود. بعد از اضافه نمودن مواد کمکی و رنگینه به غلظت دهنده خمیر حاصل به ماشین چاپ منتقل میگردد. آسانی آماده سازی غلظت دهنده از فاکتورهای مهم در انتخاب آن میباشد.
آماده سازی غلظت دهندههای نشاستهای به تورم قبلی و سپس پخت در دیگهای دوجداره احتیاج دارد. در ضمن پخت، غلظت دهنده به صورت مداوم و آرام به هم زده میشود. به هم زدن آرام غلظت دهنده از محبوس شدن هوا در آن جلوگیری مینماید. بعد از آماده شدن، لازم است که برای جدا نمودن ناخالصیها و همچنین نشاستهای که به صورت گلوله باقی مانده است، غلظت دهنده صاف گردد. (ناخالصیها میتواند به شابلونها و غلتک آسیب رساند). غلظت نشاسته لازم برای تولید ویسکوزیته مناسب ۲۵/۱۵درصد میباشد.
برای آماده سازی غلظت دهنده کتیرا، لازم است که ابتدا کتیرا به مدت ۱ تا ۲ ساعت در آب (با هم زدن) قرار گرفته و متورم شود. بعد از تورم کامل معمولا کتیرا ۲ تا ۳ ساعت جوشانده میشود و سپس صاف میگردد. در بعضی موارد مثل تهیه غلظت دهنده برای چاپ با رنگینههای خمی ممکن است کربنات پتاسیم (پتاس) را در مرحله آماده سازی غلظت دهنده به آن اضافه نمود و به این ترتیب پتاس بهتر حل و پخش میگردد. آماده سازی غلظت دهندههای طبیعی دیگر و مشتقات آنها مثل اترهای نشاسته، دانههای گیاهی به مراتب آسانتر میباشد و کافی است که پودر آنها را به مقدار مطلوب به آرامی به آبی که میکسر با دور بالا (۸۰۰ تا ۱۵۰۰ دور در دقیقه) در آن کار میکند اضافه نمود. بعد از مخلوط شدن کامل، غلظت دهنده چند ساعت میماند تا تورم لازم ایجاد شود.
جهت تهیه امولسیون نفت در آب ابتدا امولسیفایر به مقدار ۱۰-۴ گرم در لیتر در آب حل میشود. به این ترتیب که امولسیفایر به آب که میکسر در آن کار میکند اضافه شده و پس از مدت کوتاهی حدود ۸۰۰ گرم در لیتر نفت به آرامی به آب اضافه میگردد امولسیون پس از چند دقیقه آماده میشود. برای تهیه امولسیون آب در روغن (w/o) لازم است که امولسیفایر محلول در روغن، در روغن (نفت) حل شده و سپس با هم زدن شديد، تدریجاً آب به آن اضافه گردد.
امولسیون روغن در آب با آب رقیق میگردد در صورتی که امولسیون آب در روغن با آب غلیظ میشود. در صنعت چاپ بیشتر از امولسیون روغن در آب استفاده میگردد.
معایب غلظت دهنده های مصنوعی:
نسبت به غلظت دهنده طبیعی، قیمت آنها گران تر است .
سبب ایجاد زیر دست روی پارچه شده که برای رفع آن باید از نرم کن استفاده کرد.
به علت دارا بودن رنگ آن مصرف رنگ را بالا میبرد .
با بالا رفتن سختی آب مقدار مصرف آن بیشتر میشود .
در ایران بدلیل ارزانتر بودن ، مصرف رنگ پایینتر ؛ از غلظت دهنده های امولسیون استفاده میشود.
دیدگاه خود را بنویسید
مقالات مرتبط
- آمازون و سیستم تولید لباس آنلاین !
- غلظت دهنده گوار نساجی چیست ؟
- Protective Clothing on Demand
- غلظت دهنده های چاپ در نساجی
- رنگ های راکتیو Reactive Dyes
- تکمیل فرآورده های نساجی و رنگرزی(جلد 2)
- تکمیل فرآورده های نساجی و رنگرزی (جلد 1)
- تاریخچه چاپ درصنعت نساجی
- کتاب چاپ در صنعت نساجی (جلددوم)
- کتاب چاپ در صنعت نساجی (جلد 1)