chemical treatments to improve crease recovery on cotton fabric
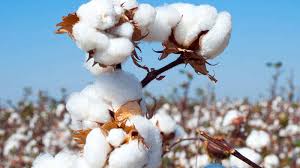
عملیات شیمیایی جهت بهبود خاصیت چروک پذیری پارچه پنبه ای Crease recovery is the property of a fabric that enables it to recover from folding deformations. It is one of the most important properties expected out of any apparel textile to make it easy to care for . Cotton is an important fibre in textiles, because of its numerous advantages. It is also one of the most comfortable fibres, so it is most commonly used for shirting fabric.
Creasing, especially after washing, is a major problem in cotton fabric because of the free hydroxyl groups in its structure. When cotton fabrics crease, molecular chains in the amorphous region slip past each other, breaking the weak hydrogen bonds because of stretched chains. They then form new hydrogen bonds in the stretched places and the fabric holds the creases. This affects the appearance of the fabric. So, cotton fabric is treated with chemicals to improve its crease recovery property.
Effect of softening agent
Softening agents give a smooth and attractive look to garments and are among the most important textile chemicals. They can make textiles supple, pliant, sleek and fluffy, smooth, more flexible and easier to drape.
Types of softeners
* Anionic softeners (sulphated oils, sulphated alcohols, soaps, oil emulsions)
* Non-ionic softeners (polyethylene emulsion, silicone emulsion, polyoxyethylene derivatives)
* Cationic softeners (quaternary ammonium and other cationic products)
Effect of anionic softener on crease recovery angle of cotton
In thick cotton fabric, crease recovery increased considerably on application of 2 per cent concentration of anionic softener. But on increasing the concentration of softener to 4 per cent and 6 per cent, crease recovery decreased.
In medium cotton fabric, crease recovery angle decreased on application of 2 per cent concentration but increased when 4 per cent concentration was applied. Treated to 6 per cent concentration, it decreased.
In case of fine cotton fabric, crease recovery angle continuously decreased on increasing concentration of anionic softener.
Effect of cationic softener on crease recovery angle of cotton fabric
Crease recovery of thick cotton fabric increased after application of cationic softener at 2 per cent concentration and on increasing concentration to 4 per cent, crease recovery decreased. Crease recovery again decreased on increasing concentration up to 6 per cent.
In case of medium weight cotton fabric, crease recovery was similar to application of anionic softener on fine cotton fabric. That shows the crease recovery angle continuously decreases on increasing concentration of cationic softener. In case of cationic softener on fine cotton fabric, crease recovery continuously decreased on increasing the concentration up to 4 per cent. On further increasing to 6 per cent, there was slight increase in crease recovery angle.
Effect of non-ionic softener on crease recovery angle of cotton fabric
After finishing cotton fabric with non-ionic softener, crease recovery of thick fabric decreased up to 2 per cent. It increased when concentration was increased to 4 per cent and then decreased when concentration softener was increased to 6 per cent of thick cotton fabric.
In medium thickness cotton fabric, crease recovery continuously decreased up to 4 per cent and increased on increasing the concentration to 6 per cent. In case of fine cotton fabric, it decreased from the control sample but it increased on increasing the concentration of non-ionic softener up to 6 per cent.
Effect of plasma treatment
Plasma treatments improve wet ability, hydrophobic finishing, adhesion, product quality and functionality of the textile material. They are a good substitute for chemical finishing as they cause no environmental pollution.
There are many gases, or mixtures of gases, used for plasma treatment. By varying the process of parameters such as type of gas, time and pressure, different finishes can be obtained. Air, nitrogen, argon, oxygen, nitrous oxide, helium, tetrafluoromethane, water vapour, carbon dioxide, methane, and ammonia or their mixtures can be used as plasma medium. Plasma treatment improves crease recovery angle on cotton fabric for all samples. A different finish shows that argon-treated sample is better than oxygen-treated sample. Treated for 40 minutes, crease recovery was better than 20 minutes.
Effect of antimicrobial finish
This type of finish is widely used in hygiene and medical sectors in textiles because antimicrobial agents are designed to kill or prevent growth of microorganisms like bacteria, fungi and viruses.
Antimicrobial finish-treated fabric shows more crease recovery angle --- 110⁰ as compare to 90.3⁰ in untreated fabric. By applying antibacterial finish to cotton fabric, crease recovery property increases slightly. During this process, starch paste in warp sheet is removed. This causes increase in the crease recovery angle. So, starch is a major factor in the grey stage which affects crease recovery.
Effect of citric acid and trisodiumcitrate on crease recovery angle of cotton fabric.The crease recovery angle decreases by increasing trisodiumcitrate concentration to the same concentration of citric acid. With increase in concentration of citric acid, crease recovery angle gradually increases.
Effect of citric acid and temperature
Increase in citric acid concentration and curing temperature directly increases crease recovery angle. But maximum concentration of citric acid and lower curing temperature show lower crease recovery angle.
Effect of trisodiumcitrate and temperature
The low concentration of trisodiumcitrate and different curing temperature shows high crease recovery angle. When concentration of trisodiumcitrate is increased, crease recovery angle is reduced. The best crease recovery angle shows during high curing temperature with high concentration of trisodiumcitrate. Crease recovery angle of cotton fabric is increased by increasing concentration of citric acid and curing temperature and trisodiumcitrate acts as the best catalyst at all concentrations of citric acid and curing temperature. Hence, citric acid was found to be one of the best cross-linking agents. High concentration of citric acid and trisodiumcitrate shows excellent crease recovery.
Effect of dimethyloldihydroxyethyleneurea (DMDHEU) and polyvinylacetate (PVAc)
DMDHEU and PVAc are used as cross linking agents. Effect of PVAc concentration shows the change of crease recovery angle of finished fabric. Dry crease recovery angle and wet crease recovery angle both are gradually reduced with increase in PVAc concentration because of the weighing and stiffing behaviour of PVAc. Effect of DMDHEU concentration shows the change of crease recovery angle of finished fabric.
Dry crease recovery angle and wet crease recovery angle both gradually increase with increase in DMDHEU concentration. Because DMDHEU can react with free hydroxyls of cellulose chains, it can convert the weak hydrogen bonds between cellulosic chains to stronger covalent bonds. Therefore, crease recovery angle of the finished fabric improved by formation of covalent cross-links between cellulosic chains.
Effect of silica nano particles
Cotton is poor increase recovery due to its free hydroxyl groups. To enhance the crease recovery property of cotton, the free hydroxyl groups are removed by cross linking agents. Silica nano particles intrude more easily into the interior of cotton fibre and adhere more tightly to the fibre structure. It was observed that increased concentration of silica nano particles contributes more to increase crease recovery angle of the fabric due to restriction of molecular movement in fibre structure.
Effect of Chitosan
Chitosan is a new range of chemicals on cotton fabric to impart protective functional advantages like antimicrobial properties, thermal resistance and protection from soiling. Comparing chitosan-treated fabric with untreated fabric and resin-treated fabric, Chitosan was treated with 0.5 per cent, 1 per cent, 1.5 per cent concentrations, varying the treatment temperature and time. Chitosan-treated fabric showed marginal increase in crease recovery angle compared to the original, untreated fabric. But angles are lower than that of resin-treated fabric. Crease recovery angle (the sum of CRA of warp way and weft way) for untreated fabric is 215⁰ and all Chitosan- treated fabrics with 0.5 per cent, 1 per cent and 1.5 per cent concentration, the crease recovery angle range up to 230⁰. The fabric treated with 1 per cent Chitosan cured at 170⁰ C shows a maximum crease recovery angle of 230⁰. Resin-treated fabric shows CRA of 265⁰. Since Chitosan treatment does not involve cross linking of cellulosic chains, these properties are considered as an added benefit beyond the gains in antimicrobial property, flame retardency and soil release property.
Effect of Nano-sized Colloidal Copper
Nano-sized colloidal copper is becoming one of the most popular chemicals in textiles with protective, functional and electronic features. Untreated cotton samples show 90⁰ crease recovery angles. Cotton treated with nano-sized colloidal copper particles shows 99⁰ crease recovery angles. Hence, there was little improvement in crease recovery angle. Therefore, though particles entered between the polymer chain molecules, they did not interfere much with polymer flexibility of the system.
Effect of poly (vinylpyrrolidone) concentration
Poly (vinylpyrrolidone) or PVP is synthetic non-toxic water-soluble polymer commonly used in a wide range of applications including pharmaceutical. It forms a film of protective colloid acting as a binder, stabiliser and complexing agents.
Crease recovery angle of treated cotton fabrics increased from 95⁰ with to 211⁰ after cross linking with glyoxal and in absence of PVP. CRA is further increased upon addition of PVP to the finishing formulation and reached its maximum value at 245⁰ upon addition of 30 g/L PVP. Further increase in PVP concentration slightly decreased CRA of the treated cotton fabric.
About the authors
R. N. Narkhedkar and Raju K. Kupelur are professors with the D.K.T.E'S textile and Engineering Institute, Ichalkaranji.
توجه : این مقاله در تحریریه سایت نساجان در دست ترجمه می باشد.
www.nasajan.com
Comment
Related articles
- کارخانه چیت تهران
- عرضه تلفیقی مواد اولیه صنعت نساجی
- نسل جدید ماشین شانه ریسندگی : TCO 21
- رنگ قرمز دیسپرس 167 Disperse RED S-2GL
- رنگ آبی راکتیو 25 Blue H5G
- رنگ آبی راکتیو 49 Blue P3R
- آمازون و سیستم تولید لباس آنلاین !
- کاربرد کریر در رنگرزی دیسپرس چیست؟
- رنگ سال 2022 کدام است ؟
- غلظت دهنده گوار نساجی چیست ؟